Einleitung
Ob Produkt- oder Prozessverbesserung, in beiden Fällen gilt für mich das (nicht ganz ernst gemeinte) Energieerhaltungsgesetz des Changemanagements:
Verbesserung heißt Veränderung
Veränderung ist Arbeit
Arbeit ist Energie
Und Energie will jeder sparen.
oder kurz gesagt:
Die Made im Speck bewegt sich nicht gerne!
(Ironikmodus aus)
"Kontinuierliche" Verbesserung lebt aber nun mal von regelmäßigen kleinen und großen, präventiven Veränderungen. Und wer in dieser Disziplin gut oder gar Exzellent sein möchte, muss Veränderung und Verbesserung zu seiner Kernkompetenz entwickeln. Auch wenn scheinbar alles gerade so gut läuft!
Die Schlüsselfrage ist nun, wie schaffen wir es, dass die Mitarbeiter ihre Energie, Zeit und Arbeitskraft gerne investieren, damit sie selbständig (selbst und ständig!) bereit sind ihre eigenen Produkte und Prozesse zu verändern und zu verbessern?
Mitarbeiter investieren in der Regel unaufgefordert Energie zur Veränderung oder Verbesserung,
-
wenn sie Spaß an der Veränderung haben
-
wenn sie einen Sinn darin sehen ihre Energie zu investieren
-
wenn es "ihr" Prozess ist oder sich verantwortlich fühlen
-
wenn sie einen Nutzen für sich oder das Ganze sehen
-
wenn ihnen Vertrauen entgegengebracht wird das Richtige zu tun.
-
wenn Transparenz besteht, was ihr tun bewirkt (im positiven und negativen Sinne)
-
wenn Fehler und Verbesserungspotential wertschätzend kommuniziert wird.
-
wenn ihnen nicht ständig jemand sagt was sie zu tun haben (fremdbestimmt vs. eigenbestimmt)
Nachhaltige Verbesserung resultiert jedoch immer aus partnerschaftlicher Zusammenarbeit und Teamarbeit. Aus diesen Grund präferiere ich zwei wesentliche Vorgehensweisen um eine gelebte Verbesserungskultur in Ihrer Organisation zu implementieren.
1) Reaktiv: Fehlermanagement und Produkt- und Prozessverbessserung mit 8D- und 5-Why-Methode
Oft ist es noch so, dass Organisationen präventive Verbesserung als notwendiges Übel ansehen. Reaktives Handeln im Fehlerfall in der Produktion oder Richtung Kunde ist dann angesagt. Fehler behoben - Problem scheinbar abgestellt. Aber wurde auch untersucht, was die Ursache war und wie es überhaupt zum Fehler kommen konnte? Wer nicht die Ursache kennt, kann auch nicht verhindern, dass der Fehler wieder auftritt. Die Verbesserung ist in solchen Fällen gleich Null! Die 8D-Systematik in Verbindung mit 5-Why-Methode führt Problemlösungsteams strukturiert zu den Ursachen und wirksamen Abstellmaßnahmen. Perfekter Abschluß ist dann die Rückführung dieser Fehler, Ursachen und Abstellmaßnahmen in eine Master FMEA, womit ähnliche Fehler in zukünftigen Entwicklungen zuverlässig ausgeschlossen werden.
Hierzu biete ich Beratung zur Implementierung oder folgende Workshops und Seminare an:
Reklamationsmanagement, 8D-Methode, 5 Why Methode
2) Präventiv: Prozessverbesserung mit interdisziplinären Teams
Es gibt ja nicht nur die Verbesserung im Fehlerfall am Produkt, die sich letztendlich in Ihren Reklamations- und Qualitätskostenstatistiken widerspiegeln. Der weitaus größere Hub zur Verbesserung liegt in den indirekten Prozessen und Abläufen Ihrer Organisation denn dort liegen 80% der Ursachen, welche in der Produktion zum Fehler führen. Hier ist das Ziel effizientes und effektives Arbeiten zu ermöglichen, die verschiedenen Arten von Verschwendung zu beseitigen und qualitativ hochwertige Produkte zu entwickeln. Das positive hier ist: Sie können das alles ohne den Stress eines Reklamationsfalles oder mit dem Kunden im Nacken tun! Sie müssen es nur wollen!
Hierzu biete ich Beratung zur Implementierung oder folgende Workshops und Seminare an:
Prozessmanagement & -entwicklung
8 D und 5 Why
Methodik im Reklamationsprozess
Fehler sind eigentlich nichts Schlimmes, wenn Sie es verstehen aus dem Fehler zu lernen und nachhaltige Abstellmaßnahmen daraus abzuleiten. Eine nachhaltige Verbesserung aus einem Fehler wird nur erreicht, wenn sich die Abstellmaßnahme gegen die Systemursache richtet und nicht gegen den Fehler. Letzteres ist "nur" eine Sofortmaßnahme um das Produkt zu korrigieren und den Kunden zufriedenzustellen. Im konkreten Fehlerfall ermitteln Sie die Systemursache am besten mit der 8-D und 5-Why-Methode.
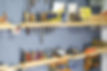
